(Um-) Baubericht VT 51 der Brohltal-Eisenbahn in 1:87 aus BS
Verfasst: 18. Februar 2013, 18:37
Vor kurzem hatte ich hier
http://www.schmalspur-modell.at/viewtopic.php?t=9371
ein Modell des DWK-Triebwagens aus dem Hause Burmester in der Ausführung als T07 der Südharz-Eisenbahn vorgestellt. Das Modell war offensichtlich als Fertigmodell von Burmester ausgeliefert und von seinem früheren Besitzer massiv gealtert worden. Der Zustand machte die Entscheidung leicht, daraus etwas Neues zu schaffen.
Entstehen sollte ein Modell entweder nach Vorbild der Köln Bonner Eisenbahnen oder der Brohltalbahn. Sehr einprägsam ist die bekannte Aufnahme von Carl Bellingroth, der den Triebwagen VT 51 der Brohltalbahn im Bahnhof Brohl in den Fünfziger Jahren zeigt (die ich aber aus urheberrechtlichen Gründen hier leider nicht einstellen kann), weshalb die Entscheidung auf die Brohltalbahn fiel. Bei genauerem Hinsehen kann man erkennen, daß dem Triebwagen im Laufe der Zeit einige Anbauten spendiert worden sind, wodurch er sich vom Auslieferungszustand und auch von der Variante der Südharz Eisenbahn deutlich unterscheidet. Neben einer Aufarbeitung gab es also an dem Modell auch eine Reihe von Änderungen auszuführen. Das Ergebnis sieht momentan so aus:








Nachfolgend darf ich wieder einmal aus einem Baubericht des Erbauers bzw. Umbauers MR zitieren:
„ I. Selbstgebaute Teile
1. Kühler
Dieser ist aus 1,5 mm dicken Messing gefräst. Die Kühlerlamellen sind mittels Diamanttrennscheibe etwa 0,2 mm tief in der Fräsrichtung in einem Abstand von 0,25 mm eingeschliffen. Nach verschiedenen anderen Versuchen ergab sich damit der beste optische Effekt. Der Rahmen um die Kühler herum ist ein 0,2 mm dicker Messingblechstreifen die Streben oben sind 0,4er Messingdraht, an den Enden plattgedrückt, durchbohrt und mittels Drahtstückchen am Kühler und Front verlötet, dann mittig mittels Schere durchtrennt. Der Ausgleichsbehälter ist ein Messing Rechteckprofilstück, das mittels Blechstreifen an die Kühlerrückseite gelötet ist.

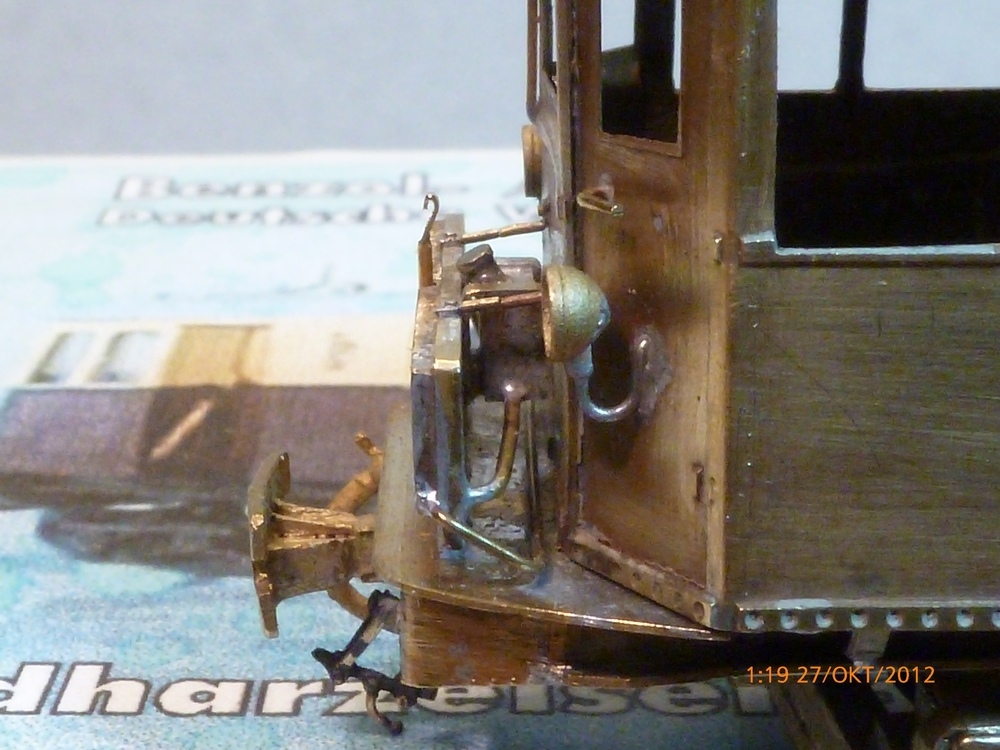
2. Bodenbleche und Rahmenverlängerung
Diese waren nötig, da beim Originalmodell die Pufferbohlen mit den Stirnseiten bündig abschließen. Nach den mir vorliegenden Bildern ist das falsch. Der Rahmen muß länger sein als das Gehäuse. Daher war die Anfertigung von neuen Bodenblechen aus 0,3 mm Messingsblech nötig, sowie entsprechende Rahmenverlängerungen aus U-Profil. Die Pufferbohle mußte entsprechend angepasst werden. Die nunmehr viel zu langen Mittelpuffer wurden durch passende ersetzt. Da auf eine Kupplungsmöglichkeit verzichtet werden konnte, war die Anbringung von Bremsschläuchen und Schraubenkupplungen möglich.

3. Dachauf- und Anbauten
Leider ist das originale Resin-Dach – na sagen wir mal unschön. Nach Entfernung aller mit angegossenen Teile und später beschriebenen Modifikationen konnte Passenderes angebaut werden, als da wären die Lautsprecher (ich hoffe zumindest, daß es auch wirklich solche waren). Diese sind aus Kugelschreiberminenspitzen herausgesägte Teile. Sofern die Minen nicht 100 % leer sind, eine „nette“ Sauerei… Dann die runden Teile unter den Lüftern (vermutlich Klappdeckel), abgesägt von Messing-Rundmaterial. Daran seitlich Ansätze aus 1 mm Messingsdrahtstücken. Stirnseitig darin eingelassene Stücke aus 0,4er Draht als Mutternimitationen. Die Lüfterklappen dahinter bestehen aus 0,8 mm dicken Kunststoffstücken – ein kleineres unten, das größere darauf. Die Dachrinne besteht aus Messingsblechstreifen 0,2 × 0,8 mm, an welche die im Dach eingeklebten 0,4 mm Drahtstückchen angelötet sind. Glücklicherweise ist der Dachkunststoff ziemlich temperaturfest, daher geht das recht gut. Die jeweiligen Enden der Blechstreifen sind an den „Fallrohren“ angelötet, die im Dach verklebt sind. Zusätzlich sind die Blechstreifen noch am Dach mit Sekundenkleber angeklebt. Die Sonnenblenden sind auf 0,4 mm Stahldraht aufgelötet, der an den Enden abgewinkelt ist. Das hält besser. Gehalten und gelagert sind diese Wellen von an den Enden plattgedrückten und durchbohrten 0,5 mm Messingsdrahtstücken, die im entsprechenden Dachbuchungen eingedrückt sind. Das ist ausreichend fest und erlaubt die Verstellung der Blenden – auch wenn das nicht unbedingt von vonnöten…
Ein Problem waren die Dachlüfter. Immerhin waren zehn Stück vonnöten, aber wie machen? Naheliegend waren Abgüsse aus Kunststoff in einer selbst gemachten Form. Zweikomponentenmaterial wäre infrage gekommen. Jedoch hätte das eine Menge Abfall ergeben, da ja doch immer wesentlich mehr angerührt als verbraucht wird. Obendrein hätte das auch recht lange gedauert (bei nur einer Form). Da kam mir ein neues Material namens „Bondic“ gerade recht. Es handelt sich um einen durchsichtigen, ziemlich dünnflüssigen Kunststoff, der mittels mitgelieferte UV Lampe (LED) angeleuchtet wird und dann in Sekunden aushärtet. Also genau das Richtige. Fehlte nur die Form. Diese besteht aus einem Stück Kugelschreibermine, daß ich am Ende mittels Reißnadel – oder genauer gesagt dem konischen Ende derselben – aufgeweitet habe. Dann wird das Minenende 5 mm lang abgesägt, das andere Ende aufgeweitet und das Rohrstück längst durchsägt. Damit sind im Prinzip zwei Formen fertig. Zum Gießen wird eine Form längs (also an den Enden) im Schraubstock oben bündig eingespannt und kann nun bis zum Rand gefüllt werden. Danach kurz beleuchten – zur Entnahme fertig! Allerdings sollte die Form vorher mit irgend einem Trennmittel (z.B. Wachs oder Öl) behandelt werden. Die so entstandenen Teile können nun auf das Dach geklebt werden, was mit dem selben Kunststoff sehr gut geht, da die „Lüfter“ ja durchsichtig sind. Also in aller Ruhe positionieren, kurz beleuchten, fest. Patente Sache.



4. Kondenswasserabscheider
Dieser besteht aus 1 x 2 mm Rechteckprofil, in das die Bohrungen vor dem Ablängen per Hand eingebracht wurden, und zwar durchgängig. Am genauesten wird es, wenn die Bohrungen jeweils bis etwa Teilemitte von beiden Seiten her gemacht werden. Wenn man sorgfältig genug war, dann treffen sich die Löcher in der Mitte…
5. Seitliche Kühlschlange
Sicherlich das aufwendigste Teil, das aus zwei Rohrgruppen besteht, die aus jeweils drei parallel verbundenen Rohren bestehen, die übereinander angeordnet sind. Es war also nichts mit langem, mäaderförmig gebogenem Draht, wie sonst üblich. Ich habe hin und her überlegt, wie dieses Ding am besten zu bauen ist. Da es zu einer längeren Beschreibung führen würde, wollte ich alles erklären, begnüge ich mich mit der Aufzählung der Eckdaten, sozusagen. Es sind also 27 Einzelteile, für die 42 Bohrungen notwendig waren, alle 0,4 mm Durchmesser. daß allein die Planung hierfür eine Weile gedauert hat, muß wohl nicht weiter erwähnt werden.



6. Unterflurrahmen mit Motorimitation




Zu deren Nachbildung gaben mir die zur Verfügung stehenden Bilder nicht viel her. Daher ist der Motor ziemlich stilisiert. Allerdings sehr viel anders kann es nicht gewesen sein, das ließen schon die beengten Platzverhältnisse nicht zu. Daher dürfte das Motorgewicht wohl zu einer Schlagseite des Triebwagens geführt haben, das man, so vermute ich, durch einen Wasserballastkasten ausgeglichen hat.
7. Wasserballastkasten
Dieser Kasten, der offensichtlich keinerlei Klappen hat, gab mir zunächst Rätsel auf. Bei der Nachbildung des Motors fiel mir dann das Vergleichsgewicht auf, was mich auf den Zweck des Kastens brachte, zumal da nur zwei Leitungen hineinführten und sonst nichts. Im Modell besteht er aus einem speziell angepassten Messingfrästeil, daß direkt an den Gehäuseboden gelötet ist. Die Nietenbänder bestehen aus etwas dicken Alufolie, 0,1 mm dick. Die Nieten habe ich mit meiner selbstgebauten Prägevorrichtung eingebracht. Die Bänder sind mit Sekundenkleber befestigt.


8. Zusatztank
Auf den Bildern ist schwach so etwas wie ein mittig angebrachter Tankstutzen zu sehen, daher meine Vermutung. Das Modell ist wiederum ein Messingfrästeil, wobei die Rundung zum Teil gefeilt wurde. Die Bänder sind aus Kupferfolie, ebenso die L-Winkel. Der Tank ist am Wagenkasten angelötet.

9. Griffe und Griffstangen
Diese waren eher angedeutet und auch falsch positioniert. Schwierig war das Bohren der Löcher neben den Türen. Das ging auch nur schräg angesetzt mit lang angespannte Bohrer – sehr abbruchgefährdend. Ist aber gut gegangen.
10. Alle zusätzlichen Leitungen
Das Problem war hier die Biegerei und das Einpassen. Mühsame Sache. So, nun komme ich zu den modifizierten Teilen.
II. Modifizierte Teile
1. Gehäusefronten
Da das Gehäuse an den Enden aus sehr dünnem Blech besteht, habe ich zur Stabilisierung aus 1 x 1 mm Messingprofil zwei Hilfsrahmen gebogen und oben bündig innen angelötet. Die Schwierigkeit lag hier in der Erzielung der genauen Biegewinkel. Auch waren sie zur stabilen Befestigung der Schlußlampenhalter und der Stirnlampen unerläßlich.
2. Untere Lampen
Diese bekamen vorbildentsprechende Befestigungsbügel aus 0,4er Stahldraht. Das ist filigran und doch stabil.

3. Gehäusebefestigung
Diese erfolgte ursprünglich mittels vier Schrauben, die nur bei abgenommenen Dach und dann nur mühsam erreichbar waren. Nur von unten durch zwei Schrauben vorn und hinten. Die Rahmenverlängerungen schafften den Platz dafür.
4. Zurückgesetzte Drehgestelle
Auf den Vorbildfotos ist zu erkennen, daß der Drehgestellabstand des Originals wesentlich geringer ist, als der des Modells (umgerechnet natürlich…). Dies ließ sich im Modell wegen Platzproblemen beim Motordrehgestell nicht ganz umsetzen. Mit einigen Tricks bei diesem (z.B. leicht zurückgezogene Zwischenwand) war es möglich, die Drehpunkte bis zur Mitte der Türen zurückzuversetzen. Damit war es dann auch möglich, die Aufstiege von den Drehstellen an den Rahmen zu versetzen, wo sie auch hingehören. Dennoch ist es noch möglich, den Roco-Standardradius ohne Klemmer zu befahren.




5. Stromabnahme
Diese ist praktisch neu aufgebaut und kommt fast ohne Verdrahtung aus. Insbesondere gibt es kein Drahtgefummel mir im Innenraum. Auf die optional von Burmester vorgesehene Innenbeleuchtung konnte verzichtet werden. Die Litzen zum Motordrehgestell hin sind nun steckbar.
6. Führerstandsinneneinrichtung
Diese wurde auf die eigentlichen Fahrpulte reduziert. Die Nachbildungen der ursprünglichen Motorabdeckungen konnten entfallen, natürlich auch die Motor-/Kühlervorbauten des Originalmodells.
7. Seitenfensterrahmen
Hier konnten bei jedem zweiten Fenster die Rahmen der Klappenster entfallen.
8. Hintere Zwischenwand
Diese (zwischen Führerstand und Einstiegsbereich) war arg gekürzt um dem Motor genügend Bewegungsfreiheit zu geben. Durch die Drehgestell-Zurückversetzung war eine Verlängerung nach unten möglich.

9. Dach
Dieses war etwas zu kurz und zu breit. Ein eingeklebter 2 mm dicker Kunststoffstreifen verlängert das Dach soweit, daß die stirnseitigen Konturen ausgearbeitet werden konnten. Zudem war es ungleichmäßig hoch, daher habe ich es erst mal planiert, dann untergefüttert mittels 0,5er Polystyrol. Das reichte schon, um genügend „Fleisch“ für eine entsprechende Konturbearbeitung zu haben. Zeitlich war durch die zu eh zu große Breite genug Material dafür vorhanden. Leider schmiert das Resin-Material ziemlich beim Schleifen und setzt Ruckzuck das Schmirgelleinen zu. Letztendlich ging es mit einer Ziehklinge (Ceranfeldschaber geht ganz gut) noch am besten. Es war jedenfalls eine schöne Geduldsprobe.“

Soweit der Umbaubericht von MR. Bis zum Lackieren wird es noch eine Weile dauern, dazu müssen erst mildere Außentemperaturen herrschen. Fortsetzung folgt.
Viele Grüße
Ralf
http://www.schmalspur-modell.at/viewtopic.php?t=9371
ein Modell des DWK-Triebwagens aus dem Hause Burmester in der Ausführung als T07 der Südharz-Eisenbahn vorgestellt. Das Modell war offensichtlich als Fertigmodell von Burmester ausgeliefert und von seinem früheren Besitzer massiv gealtert worden. Der Zustand machte die Entscheidung leicht, daraus etwas Neues zu schaffen.
Entstehen sollte ein Modell entweder nach Vorbild der Köln Bonner Eisenbahnen oder der Brohltalbahn. Sehr einprägsam ist die bekannte Aufnahme von Carl Bellingroth, der den Triebwagen VT 51 der Brohltalbahn im Bahnhof Brohl in den Fünfziger Jahren zeigt (die ich aber aus urheberrechtlichen Gründen hier leider nicht einstellen kann), weshalb die Entscheidung auf die Brohltalbahn fiel. Bei genauerem Hinsehen kann man erkennen, daß dem Triebwagen im Laufe der Zeit einige Anbauten spendiert worden sind, wodurch er sich vom Auslieferungszustand und auch von der Variante der Südharz Eisenbahn deutlich unterscheidet. Neben einer Aufarbeitung gab es also an dem Modell auch eine Reihe von Änderungen auszuführen. Das Ergebnis sieht momentan so aus:








Nachfolgend darf ich wieder einmal aus einem Baubericht des Erbauers bzw. Umbauers MR zitieren:
„ I. Selbstgebaute Teile
1. Kühler
Dieser ist aus 1,5 mm dicken Messing gefräst. Die Kühlerlamellen sind mittels Diamanttrennscheibe etwa 0,2 mm tief in der Fräsrichtung in einem Abstand von 0,25 mm eingeschliffen. Nach verschiedenen anderen Versuchen ergab sich damit der beste optische Effekt. Der Rahmen um die Kühler herum ist ein 0,2 mm dicker Messingblechstreifen die Streben oben sind 0,4er Messingdraht, an den Enden plattgedrückt, durchbohrt und mittels Drahtstückchen am Kühler und Front verlötet, dann mittig mittels Schere durchtrennt. Der Ausgleichsbehälter ist ein Messing Rechteckprofilstück, das mittels Blechstreifen an die Kühlerrückseite gelötet ist.

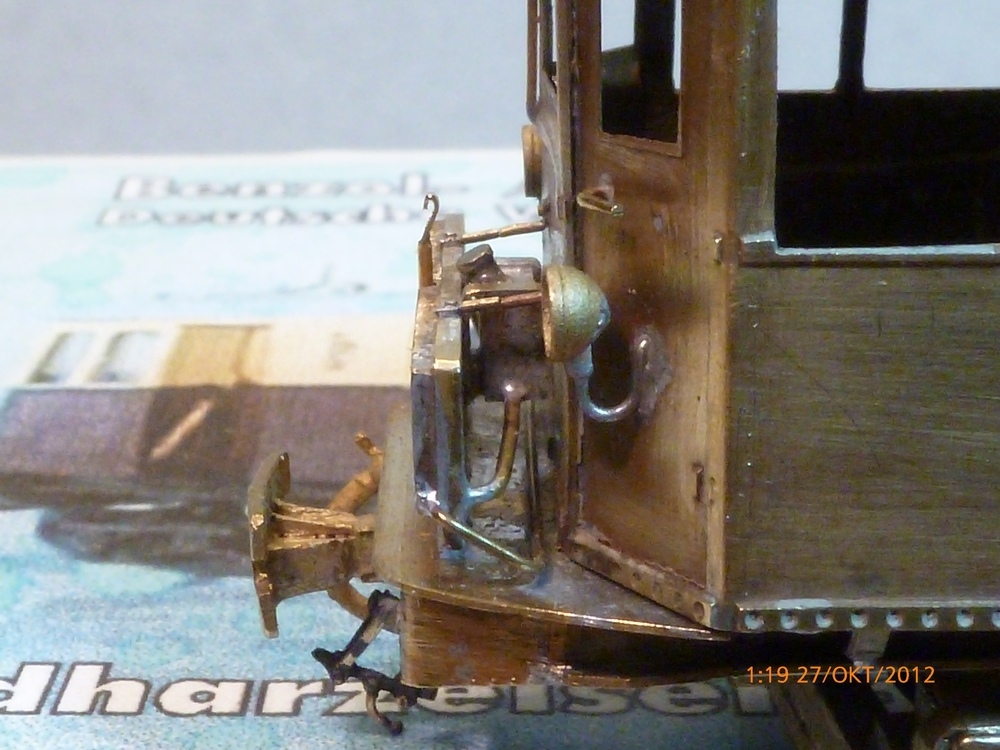
2. Bodenbleche und Rahmenverlängerung
Diese waren nötig, da beim Originalmodell die Pufferbohlen mit den Stirnseiten bündig abschließen. Nach den mir vorliegenden Bildern ist das falsch. Der Rahmen muß länger sein als das Gehäuse. Daher war die Anfertigung von neuen Bodenblechen aus 0,3 mm Messingsblech nötig, sowie entsprechende Rahmenverlängerungen aus U-Profil. Die Pufferbohle mußte entsprechend angepasst werden. Die nunmehr viel zu langen Mittelpuffer wurden durch passende ersetzt. Da auf eine Kupplungsmöglichkeit verzichtet werden konnte, war die Anbringung von Bremsschläuchen und Schraubenkupplungen möglich.

3. Dachauf- und Anbauten
Leider ist das originale Resin-Dach – na sagen wir mal unschön. Nach Entfernung aller mit angegossenen Teile und später beschriebenen Modifikationen konnte Passenderes angebaut werden, als da wären die Lautsprecher (ich hoffe zumindest, daß es auch wirklich solche waren). Diese sind aus Kugelschreiberminenspitzen herausgesägte Teile. Sofern die Minen nicht 100 % leer sind, eine „nette“ Sauerei… Dann die runden Teile unter den Lüftern (vermutlich Klappdeckel), abgesägt von Messing-Rundmaterial. Daran seitlich Ansätze aus 1 mm Messingsdrahtstücken. Stirnseitig darin eingelassene Stücke aus 0,4er Draht als Mutternimitationen. Die Lüfterklappen dahinter bestehen aus 0,8 mm dicken Kunststoffstücken – ein kleineres unten, das größere darauf. Die Dachrinne besteht aus Messingsblechstreifen 0,2 × 0,8 mm, an welche die im Dach eingeklebten 0,4 mm Drahtstückchen angelötet sind. Glücklicherweise ist der Dachkunststoff ziemlich temperaturfest, daher geht das recht gut. Die jeweiligen Enden der Blechstreifen sind an den „Fallrohren“ angelötet, die im Dach verklebt sind. Zusätzlich sind die Blechstreifen noch am Dach mit Sekundenkleber angeklebt. Die Sonnenblenden sind auf 0,4 mm Stahldraht aufgelötet, der an den Enden abgewinkelt ist. Das hält besser. Gehalten und gelagert sind diese Wellen von an den Enden plattgedrückten und durchbohrten 0,5 mm Messingsdrahtstücken, die im entsprechenden Dachbuchungen eingedrückt sind. Das ist ausreichend fest und erlaubt die Verstellung der Blenden – auch wenn das nicht unbedingt von vonnöten…
Ein Problem waren die Dachlüfter. Immerhin waren zehn Stück vonnöten, aber wie machen? Naheliegend waren Abgüsse aus Kunststoff in einer selbst gemachten Form. Zweikomponentenmaterial wäre infrage gekommen. Jedoch hätte das eine Menge Abfall ergeben, da ja doch immer wesentlich mehr angerührt als verbraucht wird. Obendrein hätte das auch recht lange gedauert (bei nur einer Form). Da kam mir ein neues Material namens „Bondic“ gerade recht. Es handelt sich um einen durchsichtigen, ziemlich dünnflüssigen Kunststoff, der mittels mitgelieferte UV Lampe (LED) angeleuchtet wird und dann in Sekunden aushärtet. Also genau das Richtige. Fehlte nur die Form. Diese besteht aus einem Stück Kugelschreibermine, daß ich am Ende mittels Reißnadel – oder genauer gesagt dem konischen Ende derselben – aufgeweitet habe. Dann wird das Minenende 5 mm lang abgesägt, das andere Ende aufgeweitet und das Rohrstück längst durchsägt. Damit sind im Prinzip zwei Formen fertig. Zum Gießen wird eine Form längs (also an den Enden) im Schraubstock oben bündig eingespannt und kann nun bis zum Rand gefüllt werden. Danach kurz beleuchten – zur Entnahme fertig! Allerdings sollte die Form vorher mit irgend einem Trennmittel (z.B. Wachs oder Öl) behandelt werden. Die so entstandenen Teile können nun auf das Dach geklebt werden, was mit dem selben Kunststoff sehr gut geht, da die „Lüfter“ ja durchsichtig sind. Also in aller Ruhe positionieren, kurz beleuchten, fest. Patente Sache.



4. Kondenswasserabscheider
Dieser besteht aus 1 x 2 mm Rechteckprofil, in das die Bohrungen vor dem Ablängen per Hand eingebracht wurden, und zwar durchgängig. Am genauesten wird es, wenn die Bohrungen jeweils bis etwa Teilemitte von beiden Seiten her gemacht werden. Wenn man sorgfältig genug war, dann treffen sich die Löcher in der Mitte…
5. Seitliche Kühlschlange
Sicherlich das aufwendigste Teil, das aus zwei Rohrgruppen besteht, die aus jeweils drei parallel verbundenen Rohren bestehen, die übereinander angeordnet sind. Es war also nichts mit langem, mäaderförmig gebogenem Draht, wie sonst üblich. Ich habe hin und her überlegt, wie dieses Ding am besten zu bauen ist. Da es zu einer längeren Beschreibung führen würde, wollte ich alles erklären, begnüge ich mich mit der Aufzählung der Eckdaten, sozusagen. Es sind also 27 Einzelteile, für die 42 Bohrungen notwendig waren, alle 0,4 mm Durchmesser. daß allein die Planung hierfür eine Weile gedauert hat, muß wohl nicht weiter erwähnt werden.



6. Unterflurrahmen mit Motorimitation




Zu deren Nachbildung gaben mir die zur Verfügung stehenden Bilder nicht viel her. Daher ist der Motor ziemlich stilisiert. Allerdings sehr viel anders kann es nicht gewesen sein, das ließen schon die beengten Platzverhältnisse nicht zu. Daher dürfte das Motorgewicht wohl zu einer Schlagseite des Triebwagens geführt haben, das man, so vermute ich, durch einen Wasserballastkasten ausgeglichen hat.
7. Wasserballastkasten
Dieser Kasten, der offensichtlich keinerlei Klappen hat, gab mir zunächst Rätsel auf. Bei der Nachbildung des Motors fiel mir dann das Vergleichsgewicht auf, was mich auf den Zweck des Kastens brachte, zumal da nur zwei Leitungen hineinführten und sonst nichts. Im Modell besteht er aus einem speziell angepassten Messingfrästeil, daß direkt an den Gehäuseboden gelötet ist. Die Nietenbänder bestehen aus etwas dicken Alufolie, 0,1 mm dick. Die Nieten habe ich mit meiner selbstgebauten Prägevorrichtung eingebracht. Die Bänder sind mit Sekundenkleber befestigt.


8. Zusatztank
Auf den Bildern ist schwach so etwas wie ein mittig angebrachter Tankstutzen zu sehen, daher meine Vermutung. Das Modell ist wiederum ein Messingfrästeil, wobei die Rundung zum Teil gefeilt wurde. Die Bänder sind aus Kupferfolie, ebenso die L-Winkel. Der Tank ist am Wagenkasten angelötet.

9. Griffe und Griffstangen
Diese waren eher angedeutet und auch falsch positioniert. Schwierig war das Bohren der Löcher neben den Türen. Das ging auch nur schräg angesetzt mit lang angespannte Bohrer – sehr abbruchgefährdend. Ist aber gut gegangen.
10. Alle zusätzlichen Leitungen
Das Problem war hier die Biegerei und das Einpassen. Mühsame Sache. So, nun komme ich zu den modifizierten Teilen.
II. Modifizierte Teile
1. Gehäusefronten
Da das Gehäuse an den Enden aus sehr dünnem Blech besteht, habe ich zur Stabilisierung aus 1 x 1 mm Messingprofil zwei Hilfsrahmen gebogen und oben bündig innen angelötet. Die Schwierigkeit lag hier in der Erzielung der genauen Biegewinkel. Auch waren sie zur stabilen Befestigung der Schlußlampenhalter und der Stirnlampen unerläßlich.
2. Untere Lampen
Diese bekamen vorbildentsprechende Befestigungsbügel aus 0,4er Stahldraht. Das ist filigran und doch stabil.

3. Gehäusebefestigung
Diese erfolgte ursprünglich mittels vier Schrauben, die nur bei abgenommenen Dach und dann nur mühsam erreichbar waren. Nur von unten durch zwei Schrauben vorn und hinten. Die Rahmenverlängerungen schafften den Platz dafür.
4. Zurückgesetzte Drehgestelle
Auf den Vorbildfotos ist zu erkennen, daß der Drehgestellabstand des Originals wesentlich geringer ist, als der des Modells (umgerechnet natürlich…). Dies ließ sich im Modell wegen Platzproblemen beim Motordrehgestell nicht ganz umsetzen. Mit einigen Tricks bei diesem (z.B. leicht zurückgezogene Zwischenwand) war es möglich, die Drehpunkte bis zur Mitte der Türen zurückzuversetzen. Damit war es dann auch möglich, die Aufstiege von den Drehstellen an den Rahmen zu versetzen, wo sie auch hingehören. Dennoch ist es noch möglich, den Roco-Standardradius ohne Klemmer zu befahren.




5. Stromabnahme
Diese ist praktisch neu aufgebaut und kommt fast ohne Verdrahtung aus. Insbesondere gibt es kein Drahtgefummel mir im Innenraum. Auf die optional von Burmester vorgesehene Innenbeleuchtung konnte verzichtet werden. Die Litzen zum Motordrehgestell hin sind nun steckbar.
6. Führerstandsinneneinrichtung
Diese wurde auf die eigentlichen Fahrpulte reduziert. Die Nachbildungen der ursprünglichen Motorabdeckungen konnten entfallen, natürlich auch die Motor-/Kühlervorbauten des Originalmodells.
7. Seitenfensterrahmen
Hier konnten bei jedem zweiten Fenster die Rahmen der Klappenster entfallen.
8. Hintere Zwischenwand
Diese (zwischen Führerstand und Einstiegsbereich) war arg gekürzt um dem Motor genügend Bewegungsfreiheit zu geben. Durch die Drehgestell-Zurückversetzung war eine Verlängerung nach unten möglich.

9. Dach
Dieses war etwas zu kurz und zu breit. Ein eingeklebter 2 mm dicker Kunststoffstreifen verlängert das Dach soweit, daß die stirnseitigen Konturen ausgearbeitet werden konnten. Zudem war es ungleichmäßig hoch, daher habe ich es erst mal planiert, dann untergefüttert mittels 0,5er Polystyrol. Das reichte schon, um genügend „Fleisch“ für eine entsprechende Konturbearbeitung zu haben. Zeitlich war durch die zu eh zu große Breite genug Material dafür vorhanden. Leider schmiert das Resin-Material ziemlich beim Schleifen und setzt Ruckzuck das Schmirgelleinen zu. Letztendlich ging es mit einer Ziehklinge (Ceranfeldschaber geht ganz gut) noch am besten. Es war jedenfalls eine schöne Geduldsprobe.“

Soweit der Umbaubericht von MR. Bis zum Lackieren wird es noch eine Weile dauern, dazu müssen erst mildere Außentemperaturen herrschen. Fortsetzung folgt.
Viele Grüße
Ralf